I
A
bicycle, ever since its discovery sometimes in 1830-40 decade,
remains the favourite personal transport of many people from all
corners of the world. In developing countries particularly, it
remains unmatched because of its low purchase cost, almost zero
running cost and very little maintenance required.
It is
believed that the first mechanically propelled 2-wheel bicycle was
built by Kirkpatrick MacMillan, a Scottish blacksmith, in 1839. Since
then, people have been trying to make changes in the bicycle design,
with very little success. The bicycles of first few decades had their
pedals directly connected to front wheel, an arrangement still used
in kid's tricycles. A bicycle with both wheels of the same size and a
chain drive with pedals provided in the middle, appeared around 1870
and has remained a standard ever since.
The
basic design of the bicycle is so perfect and good that people have
now stopped trying to make any changes to it. Designers now
concentrate more on the materials used for fabrication. We all know
that a standard bicycle is made from steel today. Though it was not
so in earlier times. The first bicycles were made of wood. After
that, manufacturers changed over to steel tubes. High tech- High end
bicycles used in racing, where weight is at a premium, use aluminium
alloys or sometimes even carbon fibers.
I want
to describe here, two types of bicycles designed from absolutely
crazy materials. The first crazy bicycle has been designed by one Mr.
Izhar Gafni, who is based in Ahituv, Israel. You might find it hard
or even impossible to believe, but he has made his bicycle from
normal cardboard. Mr. Gafni is an amateur cyclist and owns a number
of high-end bikes. He however wondered, why the original inventors of
bicycles had selected wood and decided to build a bike using wood. He
then later thought of doing even better and decided to make his bike
from something that was essentially made from wood pulp: namely
cardboard. He has spent several years now, trying to work out, how
to make a cardboard bicycle able to support the weight of a human
being. He has developed many special techniques for his bicycle
parts.
For
making the bicycle frame, he uses commercial-grade cardboard
material, made from recycled paper. The trick to increase it's
strength is in the way this cardboard is folded many times. He has
found out the exact pattern of folding required by using principles
of origami. After the cardboard is folded, he treats it with a
proprietary design resin that holds it in shape and stiffens it. He
later cuts it into the forms of the components required. After the
components are fabricated, a second application of resin makes the
component waterproof. Finally it is coated with a layer of lacquer,
which makes it look good. According to Mr. Gafni, the resulting
components are much stronger than components made from carbon fiber.
All the basic parts of the bicycle like wheels, handlebars and saddle
are made in this way, from cardboard and then fitted together.
For
making tyres, Mr. Gfni is using old car tyres. He recycles them into
solid rubber tyres, for his bicycle. In the early days, bicycle tyres
were usually made in this fashion. The ride on solid tyres is not as
comfortable as with present day pneumatic tyres, but there is no risk
of getting a puncture.
For
the chain, Mr. Gafni probably was inspired by the rubber timing belt
used in a car. His bicycle chain adopts the same design and is also
made from car-tyre rubber. The pedals are plastic recycled from empty
bottles. And the brakes are also made from some secret recycled
materials, which Mr. Gafni does not disclose.
You
would not believe it, but Mr. Gafni's finished bicycle weighs just 9
Kg and can carry a rider weighing 220 Kg. He feels that the
manufacturing cost for his bicycle should not cost more that $9-12
per unit. He thinks that not only people in poorer countries would
go for his bicycle but considering the bicycle thefts that happen in
rich nations, it may be worthwhile to buy this kind of bicycle, which
costs less than even the lock-chain arrangement used to lock present
day high cost bicycles.
I do
not know, whether Mr. Gafni would eventually find customers for his
crazy bike or not. But there is another California based designer,
who is already making bicycles from hemp and is selling them.
II
Craig Calfee is an engineer based in California. He specializes in assembly of bicycles used in bicycle racing all over the world like “Tour de France” and is considered an expert in bicycles manufactured from Aluminum and Carbon fibers. Craig has a workshop manufacturing bicycles on Pacific coast in California. However Craig is possessed for last 22 years with a craze that is something totally different than his profession. His new interest is to manufacture bicycles from Bamboo, a botanical specie that grows everywhere in the world and is classified as grasses. Craig's first bamboo frame bicycle was made about 22 years back. It worked alright except for some excess swaying.
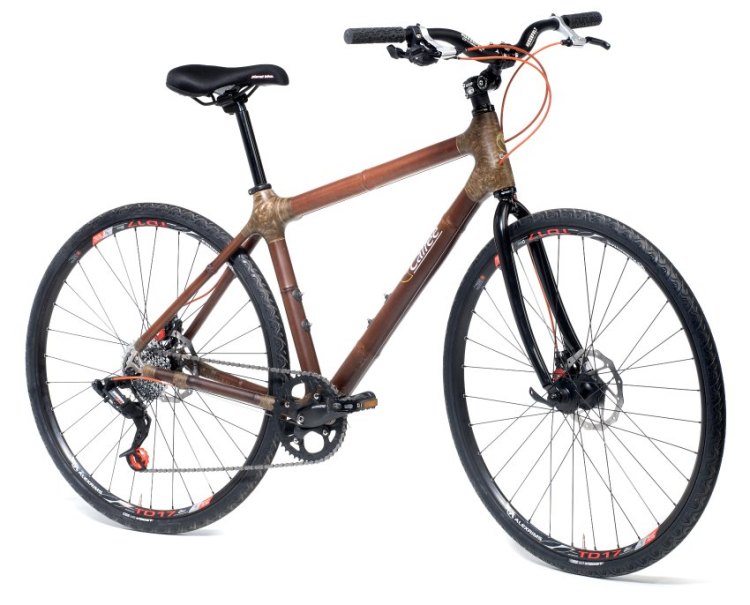
The
main difficulty in using bamboo as a raw material is its natural
tendency to crack in the middle, along its length. To overcome this
problem, Craig started smoking and heating the bamboo pieces. This
process of smoking and heating, usually called seasoning, is needed
to be carried out slowly over a period of 3 to 4 months.
To
join such bamboo pieces to each other to make a cycle frame, Craig
has developed a special process using fibers extracted from a plant
known as “ Hibiscus cannabinus.” Craig uses this fiber, coated
with Epoxy resin, to tie bamboo pieces to each other to make the
frame. Craig had to make more that 100 experimental bamboo frames for
bicycles, before he could hit on the right design. According to him,
his bamboo bicycle frame is stronger than a carbon fiber frame and
less likely to break with frontal shocks. It stands very well to the
shocks imparted to it because of the potholes and rough patches on
roads. EFBe bicycle testing laboratory from Germany has recently
carried out tests on this bicycle and has certified its quality.
Craig's
bamboo frame bicycle, in spite of it's lowest carbon foot print,
unfortunately is very expensive to make and sells for an astronomical
figure of US$ 2700, making it out of reach for anyone in developing
countries. To overcome this difficulty, Craig has commenced a project
called “Bamboosera”
in
collaboration with Columbia University. Under this project, training
is imparted to candidates from developing countries to manufacture
bamboo bicycles. Once they are trained, they are in a position to
start their own cottage industry to make these bicycles. In 2010,
“Bamboosera” trained three groups of people from African nation
of “Ghana,” to make the bicycles. This project now plans to start
these training programmes in Uganda, Liberia, Philippines and New
Zealand. Craig is also trying to develop a pedal powered but more
sturdier vehicle from bamboo that can carry one adult person along
with 4 or 5 kids.
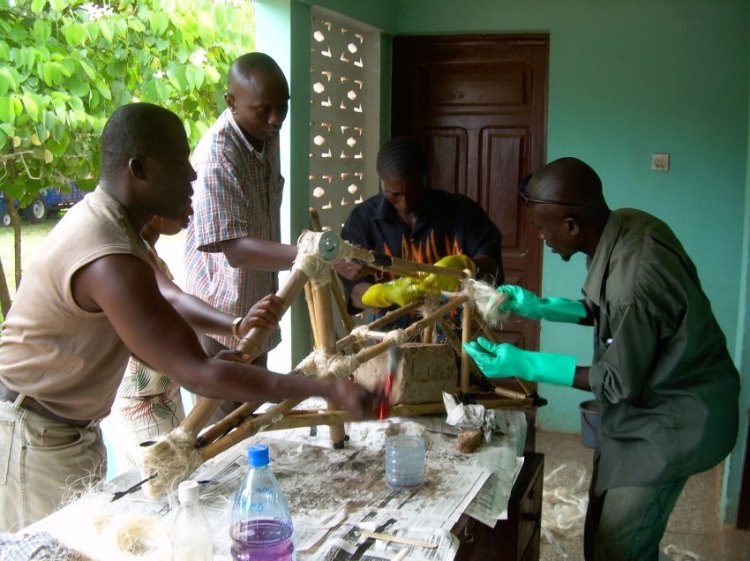
Craig
may not be the only person with a green bicycle bee in his bonnet.
Three other guys; Brano Meres from Slovak republic, another
California designer Nick Frey and Nicolas Meyer from Germany are
actively involved in the manufacture of a green bicycle. “Biomega,”
is a company from Denmark, who make a very good looking bamboo bike.
There is also an ongoing project at the Technical University of
Berlin developing similar bicycles called Berlin Bamboo Bikes. Nick
Frey's company “Boo Bicycles” now in Colorado, also specializing
in bamboo bikes.
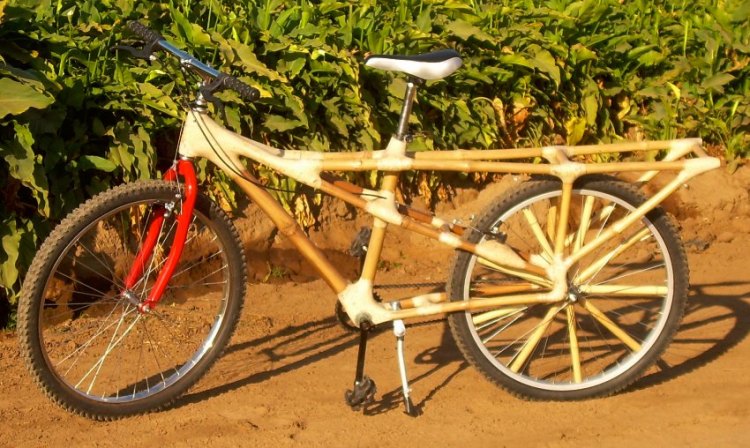
Perhaps
Nicolas Meyer from Germany has the most advanced green design for a
bicycle. His bicycle is made mainly out of hemp and bamboo. His
bicycle consists of 60% hemp, 15% bamboo and the rest is carbon and
aluminum. He gets his hemp in bulk from a hemp store and his bamboo
comes from a florist. To make the bicycle frame Meyer dips the hemp
fibers into a thermal epoxy resin and then wraps them around a
Styrofoam frame. The frame looks bit chunky because of this method
of construction. The hemp ropes can take a lot of weight. But when
there's pressure, they bend. To ensure that the saddle mounting,
which is made up of two tubes, doesn't get bent out of shape, there
is a three-centimeter wide band around the tubes. This method of
construction makes the bike more rigid, but not any heavier. It still
weighs around 1.4 kilograms, which is approximately the same as a
good aluminum bike frame. Bicycle is considered as a personal
transportation that creates least amount of pollution. Yet present
day steel bicycles consume much power, when manufactured. If a
bicycle is manufactured with least amount power and uses recycled or
recyclable raw materials, it would become the most ideal vehicle for
tomorrow.
Who knows? These crazy bamboo bicycles might become the standard some day. At least these designers seem to think so.
III
In the
first two parts of this series, we discovered crazy bicycles made from cardboard and also from Bamboo and Hemp.
I have found yet another bicycle maker now, who surprisingly uses
only normal materials used by all bicycle manufacturers; namely steel
tubes, to make his bicycles. Still, we can classify his bikes in the
crazy class, because of their price, which hover around 10K Dollars.
You
don't believe it? Well! I also did not believe it first, but after
reading about the bicycle, Mr. Po (Name changed) has purchased from
this bicycle assembler, I had to believe the story. Mr. Po, 47, is an
average Singaporean, works as a country manager for an electronics
company, is married with two children and cycles for leisure. He
belongs to a class or creed of people, whom, we can simply describe
as bicycle buffs. Every Sunday morning, he rides his bicycle for
about 42 km, along the East Coast Park.
About
2 years ago, Mr. Po decided to retire his trusty steed, a 26 year old
bicycle.
There
is nothing crazy about this. Almost all bike riders periodically
change their rides. It is pretty simple, just walk to a bicycle shop
and buy one off-the-shelf replacements and you are done. But our Mr.
Po, did not like the idea. He wanted his new bicycle to be a handmade
specimen, customised to his specifications. There are number of shops
in Singapore on Serangoon Road, who offer customised bicycles for
their clients. But they merely assemble the bicycle from standard
parts, fabricated abroad, like the frame for example that is
fabricated in the United States.
Mr. Po
went instead, to another bicycle manufacturer; Mr Suleiman, who owns
a bicycle factory in Gaylang East industrial estate in Singapore,
called as “Rebound center.” This place is one of the few local
companies, that will build a bicycle from scratch for the customers,
fabricating the steel frame right here in Singapore. Mr. Suleiman
agreed to fabricate a bicycle just the way Mr. Po wanted, but his
quotation was whooping SG$ 14000 and it would take him at least 18
months to make the bike. Mr. Po, after giving some thought to it,
decided to bite the bullet and ordered the bicycle.
Mr.
Suleiman, who owns this shop, is a frame builder who was trained for
about one and half months at the United bicycle Institute in Oregon
in the US in 1994. However, upon his return to Singapore, found that
there was little demand for custom-fabricated frames here. His shop,
which he opened in 1995, does mainly bicycle servicing and about two
custom-fabricated bicycle frames in a year. But this dropped to none,
in the late 1990s. Fortunately for him, demand for custom-fabricated
bicycles started to pick up again around six years ago. Mr Suleiman
now custom-makes about two bicycles every year, each costing between
SG Dollars 6000 and 20,000. The customers for his custom made
bicycles are usually male and female working professionals in their
30s and 40s.
Mr.Suleiman
fabricates his bicycles with great passion. His bicycle frames are
fabricated to a degree of accuracy that involves measurements of up
to one-tenth of a Millimeters and and degrees. It takes a minimum of
80 man-hours over at least six months, to build the frame and
assemble it with wheels, gears, breaks and other parts. It is obvious
that fabricating bicycle frames is not Mr Sulaiman's bread and
butter, it is a crazy job which he finds immensely enjoyable. While
explaining his passion for bicycle making, Mr Suleiman says: "It
is creative work. There is the satisfaction of making something that
can be used to ride out of nothing."
Mr. Po
got his new bicycle after waiting for almost one and half year, and
took a photograph of his own along with his new bike to remember the
occasion. He says: "when I collected it, I felt a sense of
accomplishment. For me it was realising a childhood dream that I am
able to afford at bicycle like this. This might be the last bicycle I
get, so I wanted to splurge on something that nobody has." He
adds further that the big ticket item was thoroughly worth it. He
adds: "it is unique to me. I am more comfortable riding it
because it is customised to my dimensional's."
Nothing
to beat these crazy bicycle manufacturers and riders, who will not
mind to fork out sums, in which one can buy a medium sized family
sedan in India.
----------
4.
Crazy Bicycles- Part IV
In the
earlier parts of this series, we saw some real crazy bicycles like
those made
from cardboard, bamboo
and hemp. In another part, we saw custom
made bicycles from Singapore. The crazy bicycle that I am going
to describe to you here is made like any other conventional bicycle
with the only difference that it need not be peddled around. It
actually runs on solar power.
Jesper
Frausig is a Danish solar-energy engineer, who works for Gaia Solar,
a solar-energy integration company based outside Copenhagen, where he
lives. Like most of the Danes, Jesper is an avid biker. As per
Government data, 90% percent of Danes have their own bikes and almost
36% of them use them to pedal to work every day. Frausig was always
interested in electrically powered bicycles as they are completely
pollution free. But normal electric bikes did not excite him at all
because they are very heavy and not built for young people.
With
his job as a solar engineer, Frausig had much specialised knowledge
of how solar power systems work. He decided to put this in use and
tried to come out with a bicycle that could be solar powered. He
says that his knowledge of solar power facilitated him to design a
bike with lightweight custom made components instead of what was
available readily in the market, but decided not to change the basic
two wheel design of a bicycle.
Frausig
started by mounting a 500-watt electric motor on the pedal assembly.
This would be powered by a lithium-ion battery pack, housed in a
tubular container, which was mounted on the main frame of the
bicycle. He decided that relying only on solar power to charge the
batteries would be impractical as sunlight sometimes is not available
for days in Denmark. He therefore provided a socket so that the
batteries could be charged from a household electrical outlet.
Main
solar panels to charge the batteries were fitted in form of
disc-shaped arrays mounted inside the wheel spokes. Each wheel is
capable of collecting 25 peak watts of solar energy on a sunny day.
Although in the present version, it is possible to do it only when
the bicycle is at rest. A lacuna, which Frausig wants to change in
future versions. Another problem faced by present version is because
of the solar panels having been integrated only on one side. This
puts a restriction on panels that they can receive direct sunlight
only on one side. In the present version, it can take five days to
fully charge the battery, depending on sun conditions.
Because
Frausig's bicycle has wheel mounted solar arrays, the wheels look
similar to the disc wheels used by indoor track cyclists. The main
problem with such disc wheel bicycles is that they are extremely
sensitive to crosswinds. Frausig wants to overcome this by increasing
the density of the solar cells on the rear wheel and eliminate them
completely from the front wheel.
Frausig's
bicycle is a single gear ratio bicycle that can run at 30 mph under
optimal conditions and the bicycle can run about 40 miles on a fully
charged battery. The desired speed can be set on a handlebar-mounted
control. Sensors fitted in the pedals adjust the speed of the motor
so that the motor is always supplementing the pedal power.
Frausig's
bicycle would not be available at present for customers, who might
wish to buy one. He feels that the bicycle needs lots more
improvement and wants to further improve it, before it can be made
commercially and sold to people. One thing is for sure. His bicycle
has generated much interest for two things; first being it's sporty
design with only about 19 Kg weight instead of typical e-bikes
weighing around 35 Kgs. Perhaps the most important reason for
interest of people is that it is solar powered and that is why
people stop Frausig any time, when he is riding his bicycle, and ask
him, what is he riding?
No comments:
Post a Comment